Dispensing Equipment And Global Regulatory Compliance
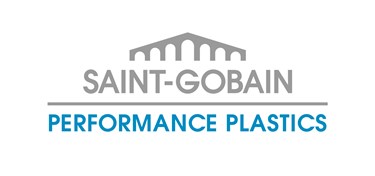
How the right tubing solution can help brand owners stay ahead of regulatory changes and ensure a consistently positive consumer experience with dispensed products
By Iuliana Nita, Global Marketing Manager, Beverage, the Process Systems Business Unit of Saint-Gobain
Whether it’s dairy products, fountain soda, hot chocolate or juice, dispensed beverage products can be found just about everywhere – with food-service workers and even consumers operating the dispensing equipment. Because of this, beverage brand owners do not always have strict control over the sanitation and maintenance processes, which can directly impact the quality, consistency and safety of products. The potential results include product inconsistency and perceived food safety issues.
In these instances, the best protection is preparation. Brand owners can ensure the dispensing equipment used for beverage products use the best tubing solutions that make cleaning easy and prevent any external flavors or substances from interfering with the product experience. The right tubing selection can prevent external particles, cleaning solutions, and leachables from entering the product stream and interfering with the flavor profile.
By specifying dispensing equipment specifically designed for durability, reliability, and to be easily cleaned, brand owners can overcome challenges presented by the lack of control they have over the operation and maintenance of these machine. The right tubing solutions can go a long way in helping to meet these performance objectives. Outfitting dispensing equipment with high-performance tubing is a critical step toward ensuring a safe and consistent product, reinforcing the positive consumer experience, as well as the brand’s values every time.
Regulators ‘Round the World
Regulations exist around the world to guard the safety of beverages served from dispensing equipment. In the U.S., the FDA is the agency regulating substances that come in contact with food. The National Sanitation Foundation (NSF) lists appropriate materials and manufacturing processes for the production of food processing equipment.
In the European Union, the Framework Regulation No 1935/2004 regulates materials intended to come into contact with food. The intent of the Framework Regulation is to ensure that foreign materials that could endanger human health, change the composition of the food product, or deteriorate the organoleptic characteristics (taste, smell, and texture) do not contaminate the product.
Japan’s Food Sanitation Law establishes a “positive list” of additives that are allowed to be used in food and beverage products. In other words, only additives that are on the list are permitted for use in foods in Japan.
Various materials, such as bisphenol A (BPA) and phthalates, continue to draw public scrutiny, with perceived consumer safety concerns driving legislation. In order to stay ahead of the curve, brand owners and Original Equipment Manufacturers (OEM) must anticipate inevitable regulatory change and specify less contentious tubing materials.
Streamlining Compliance & Food Safety Measures
Because regulations vary from region to region, it is beneficial for brand owners to use one tubing solution that complies with standards set by all major regulatory bodies. Rather than outfitting dispensing equipment in five different regions with five different types of tubing, international brand owners can work with dispensing equipment manufacturers to use one, globally compliant solution. This approach streamlines a brand owner’s supply chain, eliminates the need for multiple sets of equipment literature, and, ultimately, reduces cost.
In addition, brand owners often transfer control of sanitation and maintenance procedures to the retail and restaurant workers operating the dispensing equipment. The best defense against potential contamination issues or recalls following new legislation is to ensure that all materials comply with necessary regulations and do not contain chemicals of concern. It is also important to design equipment that limits kinking and avoids other complex configurations that make regular cleaning and maintenance difficult. Finally, providing clear maintenance and cleaning instructions to equipment users can go a long way in preventing food-handling safety issues.
Given a lack of direct control or the ability to ensure proper usage, brand owners and OEMs have a veritable laundry list of factors to consider when developing the best possible dispensing equipment to guarantee the consistency and quality of their products. Not all brand owners and OEMs have the expertise necessary to determine the best tubing solution for a dispensing application, but there is an answer. A knowledgeable component supplier can be a resource for component solutions, providing guidance on proper material selection, certainty, and peace of mind. Choosing the right supplier that can provide a variety of high-performance and high-quality solutions will help ensure that the right tubing is used for the right dispensing application. A tubing solutions supplier with comprehensive design capabilities and materials science know-how can help OEMs to design high-performance dispensing equipment that not only achieves long-term cost-savings and reduced downtime, but also protects beverage brand integrity and the consumer.
Dispensing Solutions Inside & Out
There are several factors to consider when specifying tubing material. Small components can have a major impact on the overall safe and effective operation of dispensing equipment. Tubing solutions made from a variety of high-performance polymers and other enhanced materials can offer a wide range of attributes making them ideally suited for various applications. Materials must be carefully selected based on the application to ensure the tubing performs well.
Attributes such as flexibility, durability, chemical resistance, and non-leaching attributes – in varying capacities – are critical to the success of the tubing and dispensing equipment as a whole.
Tubing designed specifically for use with solvents requires special properties in the inner bore to withstand the negative effects to taste, odor, and product purity caused by extraction from the tubing. In the case of equipment that utilizes a pressurized pump to dispense the product, different materials are needed in order to formulate tubing that can withstand constant pressure. It is important to note that the layering of materials must always comply with regulatory standards. For beverage dispensing equipment, all of these factors must be taken into account when determining the correct tubing solution.
Pump Performance
Many high performance beverage dispensing systems rely on peristaltic pump technology to control the flow of the media. Peristaltic pumps are excellent for dosing or metering chemicals, liquid ingredients and flavorings. Transferring highly viscous solids from one location to another is also an ideal application for a peristaltic pump. Food slurries are great applications for peristaltic pumps. The tubing element plays a vital role in securing the pump’s superior performance and ensuring today’s hygiene standards are met.
Chemical And Heat Resistance
In order to remain effective in beverage dispensing applications, tubing materials must be resistant to the chemicals found in the various cleaners used during sanitation processes, as well as those found in the product itself.
Depending on the beverage product, cleaner, and/or temperature to which the tube is exposed, it may require varying levels of chemical resistance. For example, products with alcoholic content, such as wine, can degrade or damage the tubing at a faster rate than products such as iced tea. In addition, tubing should be heat resistant, with high temperatures commonly found in coffees, teas, and cocoas.
Non-Leachable And Non-Porous Attributes
Certain tubing materials can be especially prone to leaching flavors, or susceptible to imparting tastes from other substances onto the product. From a safety standpoint, beverage tubing materials should not leach chemicals into the beverage product. In order to protect brand integrity, the materials must also prevent beverage particles from sticking to the inner bore, potentially jeopardizing the flavor and integrity of the next batch of product being dispensed.
About Saint-Gobain Performance Plastics
Saint-Gobain Performance Plastics is a subsidiary of Saint-Gobain, one of the top 100 industrial companies in the world and a leading producer of construction products, flat glass, high-performance materials and packaging. The Process Systems Business Unit of Saint-Gobain Performance Plastics produces critical connections through a broad range of customized material solutions and capabilities to help customers achieve safety, performance and brand assurance in the aerospace, chemical and food & beverage industries. For more information, visit http://www.plastics.saint-gobain.com/