Planning a Pigging System? What Food Processors Need to Consider
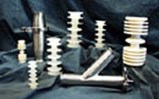
By Bryan K. Downer
Applications Specialist, Process Engineering
Central States Industrial Equipment & Service, Inc.
"Pigging systems" – A moving projectile through a piping system, usually with flexible wipers or brushes, sized larger than the consistent ID diameter of a pipe, in order to clean the pipes of residual product and/or recover product. This concept was made popular by the oil industry. However, the methods of pigging have evolved to accommodate a wide variety of industries and requirements. It is said that these pipeline projectiles claim their name from the days when barbed wire wrapped rags were sent down a pipeline to clean residual oil and gas from the inner walls. As these projectiles scraped along the inside of the pipe they produced a high-pitched resonance or swine-like "squeal", hence the name pig.
Methods/Purposes
Nearly every industry that uses tubular piping to transfer product uses some type of pig system either to recover or clean product or residue from the lines. The sanitary process industry (food, dairy, and beverage) is one of the fastest growing users of pigging systems. Due to increasing costs of raw and finished goods, producers are realizing the cost saving potential of recovering the product in their lines, which otherwise would mostly go to drain. Along with the immediate product savings, waste treatment costs also decline because there is less product wasted, line circuits are easier to clean, and the use of caustic solutions is less due to a considerably smaller amount of product in-line to neutralize the cleansers. These are among the many reasons producers are finding pigging systems to be "worth their weight in gold".
Air blowing has been a favored method for partial product removal from lines. However, it does have its downfalls. Air blowing does not evacuate the entire residual product, which may accumulate in low areas or "dead legs" and along the walls of the pipeline. In some cases the product that is left is dried or seasoned by the air and is difficult to remove with cleaning solutions. The residual product left by air blowing mixes with the cleaning solution, increasing the amount of time and solution required to thoroughly clean the line. In other cases, the product that is removed by air blowing is adversely affected by the direct high air pressure contact, rendering it useless and wasting product that must be disposed. For example, dairy cream when introduced to air blowing is whipped and air is entrained, turning the cream to the consistency of butter.
By putting a barrier between the media (air, water, etc.) and the product, the product is never exposed to the media, eliminating adverse effects. This barrier is commonly referred to as a pig or projectile. The interference fit between the pig wipers and pipe walls gives a positive seal between the media and the product causing a wiping or "squeegee" action on the inside of the smooth bore pipe or tubing. This allows for nearly all the product to be removed, leaving it intact for recovery.
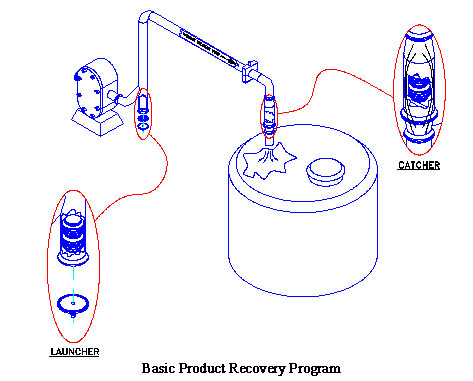
There are basically two types of pigs used in the sanitary industry; one is molded from a solid elastomer, and the other uses a hard plastic or metal body bolted together with elastomer wipers sandwiched in between.
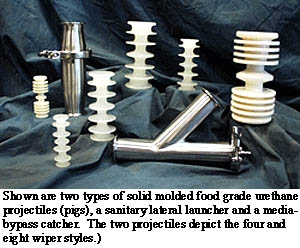
The solid molded type allows for a continuous flexible fit through direction changes in the line, by giving the body and the wipers multidirectional flexibility. The one molded piece design also allows for easy cleaning. The sectioned or "bullet" type pigs with replaceable wipers are less flexible due to their rigid body design. However, they have the advantage of being able to replace the wipers once they are worn, but they are harder to clean because of their sectioned design, and may require disassembly to fully sanitize. These sectioned projectiles are usually equipped with two wipers, whereas the solid molded versions are commonly designed with four or more wipers. This gives the solid molded projectile the added benefit of a longer service life between replacements.
Technical Data
When using or planning for a pigging system there are three main things to consider:
- 1. Pig velocity through the piping system. A good rule of thumb is to maintain 3-5-ft per second through the run, less than 3fps is usually acceptable, but in order to maintain the optimum life of the pig, the maximum should be 5fps. Pig velocity is directly proportionate to the differential pressure requirement between the system and the air or fluid media available.
- 2. Differential pressure in the system. Described as the dynamic backpressure of the moving product, versus the available pressure of the media. The dynamic pressure, or friction loss produced by the product, is based on the product viscosity, velocity, weight, line size, line length and pipe roughness. A viscous product or a long pipe run may need to be moved slower in order to reduce the initial differential pressure. As the pig evacuates the product from the line, the amount of product and line length effectively decreases, increasing the differential pressure, causing the projectile to move faster. This increase in speed in turn increases the dynamic pressure of the projectile while continuing to increase velocity exponentially.
- 3. Media pressure and volume. If media pressure and volume are effectively maintained, the increase in velocity, which can reduce projectile life, can be controlled. In order to maintain a constant media pressure as the pig moves down the pipeline, the volume of media available must be equal to or greater than the displaced product. If the media available is less than the amount of product that the pig is displacing, the effective media pressure inside the pipeline will be reduced and the pig will decrease in velocity. Also, if the media pressure is reduced at any point during the pigging cycle the pig velocity will decrease.
Another consideration when planning a pigging system is the air quality, when using compressed air as your media. 3A has recently revised its requirements for air in contact with product or product contact surfaces. If your plant's air system is not up to code, the pig system manufacturer can give you some options for localized filtration to satisfy your specific air quality requirements.
In summary, a pigging system like any other type of processing equipment must be evaluated for its desired use and specified accordingly. Product recovery system manufacturers are one of the best resources for analyzing your system and making the best recommendation for your exact application.
Central States Industrial Equipment & Service, Inc., 2700 Partnership Blvd., Springfield, MO 65803. Tel: 800-654-5635; Fax: 417-831-5314.